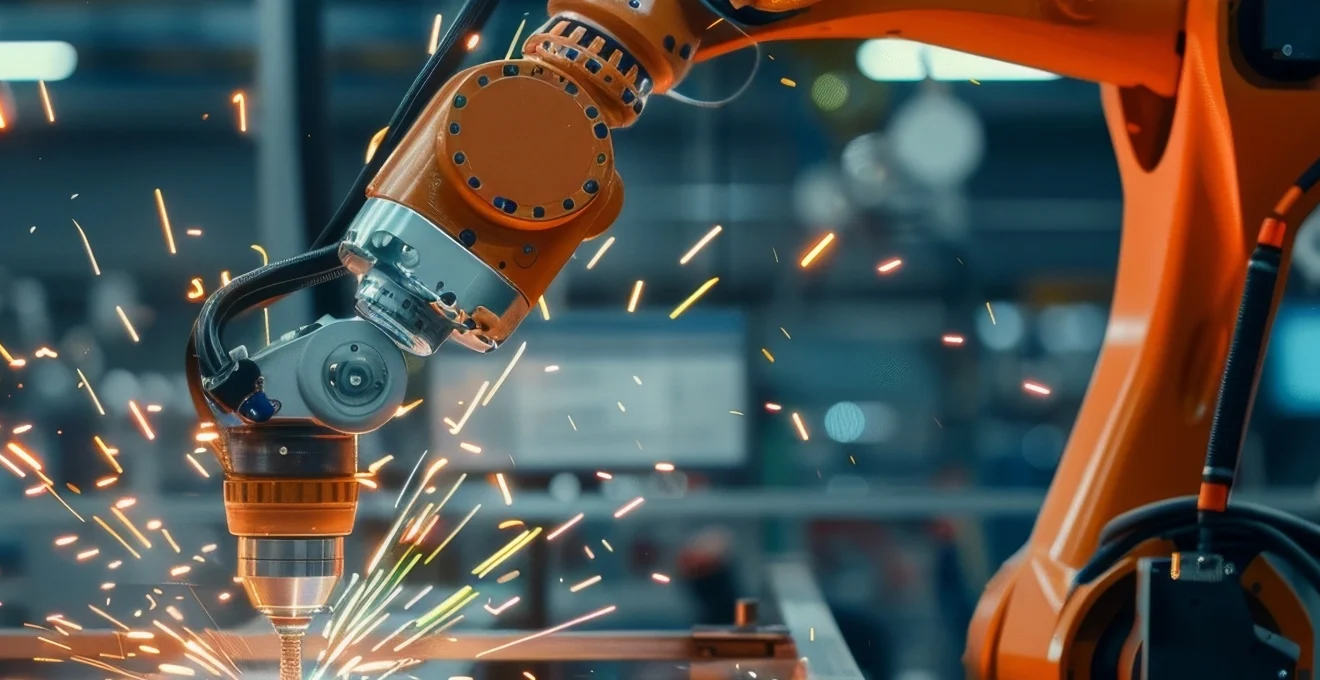
Friction stir welding (FSW) has emerged as a revolutionary joining technique for industrial applications, particularly in sectors requiring high-strength, defect-free welds. This solid-state process, which uses a rotating tool to generate frictional heat and mechanically intermix materials, has gained traction in aerospace, automotive, and marine industries. Selecting the appropriate Friction stir welder for specific industrial needs involves careful consideration of multiple factors, including material compatibility, welding capacity, and control systems. The choice of FSW equipment can significantly impact production efficiency, weld quality, and overall manufacturing costs.
Key Factors in Friction Stir Welder Selection
The selection of a friction stir welder for industrial applications necessitates a comprehensive evaluation of several technical parameters. These parameters directly influence the machine's capability to produce high-quality welds across various materials and thicknesses. Understanding these factors enables manufacturers to make informed decisions that align with their production requirements and quality standards.
Material Thickness Range and Welding Capacity
The material thickness range and welding capacity of a friction stir welder are fundamental considerations in the selection process. These parameters determine the versatility of the machine and its ability to accommodate diverse welding projects. Friction stir welders are designed to handle specific ranges of material thicknesses, typically from a few millimeters to several centimeters. The welding capacity, often expressed in terms of maximum weldable thickness, varies depending on the machine's specifications and the materials being joined. For instance, a friction stir welder capable of welding aluminum plates up to 50 mm thick may only manage 25 mm in steel due to the material's higher strength and melting point. Additionally, the welding capacity encompasses the machine's ability to maintain consistent weld quality across long seams, which is particularly relevant for applications in the aerospace and shipbuilding industries where extended weld lengths are common.
When evaluating friction stir welders, it is essential to consider not only the current production requirements but also potential future needs. Selecting a machine with a welding capacity that exceeds immediate needs can provide flexibility for future projects and potentially eliminate the need for additional equipment purchases. However, this decision must be balanced against the higher initial investment and operational costs associated with larger, more powerful machines. Furthermore, the material thickness range should be compatible with the specific alloys and materials used in the manufacturing process, as certain materials may require specialized tooling or process parameters to achieve optimal weld quality.
Spindle Power Output and Torque Specifications
The spindle power output and torque specifications of a friction stir welder are critical factors that directly impact its performance and welding capabilities. These parameters determine the machine's ability to generate sufficient frictional heat and mechanical force to plasticize and mix the materials being welded. Spindle power, typically measured in kilowatts (kW), indicates the energy output available for the welding process. Higher spindle power generally allows for welding thicker materials and harder alloys, as well as maintaining higher welding speeds. Torque, measured in Newton-meters (Nm), represents the rotational force applied by the spindle to the welding tool. Adequate torque is essential for overcoming material resistance, especially when welding high-strength alloys or large thicknesses.
When selecting a friction stir welder, it is crucial to match the spindle power and torque specifications to the intended applications. For example, welding aluminum alloys typically requires less power and torque compared to welding steel or titanium. However, even within the same material category, different grades and thicknesses may necessitate varying levels of spindle performance. A machine with insufficient power or torque may struggle to maintain consistent weld quality, potentially leading to defects such as inadequate material mixing or incomplete penetration. Conversely, over-specifying these parameters can result in unnecessary capital expenditure and higher operating costs. To optimize the selection process, manufacturers should analyze their welding requirements in terms of material types, thicknesses, and production volumes. This analysis should inform the choice of spindle specifications, ensuring that the selected friction stir welder can efficiently handle the full range of anticipated welding tasks.
Machine Rigidity and Vibration Dampening Capabilities
The rigidity of a friction stir welder and its ability to dampen vibrations are crucial factors that significantly influence weld quality and machine longevity. A rigid machine structure minimizes deflections and distortions during the welding process, ensuring that the tool maintains its intended position relative to the workpiece. This precision is particularly important in friction stir welding, where even small deviations can lead to weld defects or inconsistencies. Machine rigidity is typically achieved through robust construction, often utilizing heavy-duty steel frames and reinforced components. The design of the machine's base, columns, and spindle housing all contribute to its overall stiffness and resistance to deformation under load.
Vibration dampening capabilities complement machine rigidity by absorbing and dissipating the forces generated during the welding process. Effective vibration control is essential for maintaining weld quality, particularly when welding at high speeds or with large diameter tools. Vibrations can lead to tool wear, surface finish issues, and in severe cases, weld defects. Advanced friction stir welders incorporate various vibration dampening technologies, such as hydraulic or pneumatic isolators, tuned mass dampers, or active vibration control systems. These features help to isolate the welding process from external disturbances and minimize the transmission of vibrations through the machine structure. When evaluating friction stir welders, manufacturers should consider the specific vibration challenges associated with their applications, such as thin-walled structures or materials with high damping characteristics. Machines designed with superior rigidity and vibration control often command a premium but can provide significant benefits in terms of weld quality, tool life, and overall process stability.
Evaluating Friction Stir Welder Control Systems
The control systems of friction stir welders play a pivotal role in ensuring precise, repeatable, and efficient welding operations. These systems encompass the hardware and software components that manage the welding process, from setting and maintaining welding parameters to monitoring and adjusting machine performance in real-time. Advanced control systems can significantly enhance the capabilities of friction stir welders, enabling complex welding paths, adaptive process control, and comprehensive data collection for quality assurance purposes.
Programmable Logic Controllers for Automated Operation
Programmable Logic Controllers (PLCs) form the backbone of modern friction stir welder control systems, enabling automated and precise control over the welding process. These robust industrial computers are designed to withstand harsh manufacturing environments while providing reliable and flexible control capabilities. PLCs in friction stir welders manage a wide range of functions, including spindle speed control, axial force regulation, tool positioning, and weld path execution. The sophistication of PLC systems can vary significantly between different friction stir welder models, with more advanced systems offering features such as multi-axis synchronization for complex geometries and adaptive control algorithms that adjust welding parameters in real-time based on sensor feedback.
When evaluating friction stir welders, the capabilities of the PLC system should be closely scrutinized to ensure compatibility with production requirements. Key considerations include the processing speed of the PLC, which affects its ability to handle high-speed welding operations and respond quickly to process variations. The memory capacity of the PLC is also crucial, particularly for applications requiring storage of multiple welding programs or extensive data logging. Additionally, the input/output (I/O) capabilities of the PLC determine its ability to interface with external sensors, safety systems, and material handling equipment. Advanced PLC systems may offer features such as remote monitoring and control, allowing operators to supervise welding operations from a central control room or even off-site locations. The programming interface of the PLC is another important factor, as it affects the ease with which operators can create and modify welding programs. User-friendly programming environments with graphical interfaces and pre-built function blocks can significantly reduce setup times and minimize the risk of programming errors.
Intuitive Human-Machine Interfaces for Enhanced Usability
The Human-Machine Interface (HMI) of a friction stir welder serves as the primary point of interaction between operators and the machine, playing a crucial role in operational efficiency and user satisfaction. An intuitive HMI design can significantly reduce the learning curve for new operators, minimize the risk of errors, and enhance overall productivity. Modern friction stir welders typically feature touchscreen displays with graphical user interfaces that provide real-time visualization of welding parameters, machine status, and process data. These interfaces often incorporate color-coded elements and intuitive icons to convey information quickly and effectively, allowing operators to monitor multiple aspects of the welding process at a glance.
When evaluating friction stir welders, the design and functionality of the HMI should be carefully considered. Key aspects to assess include the clarity and organization of information presented on the screen, the responsiveness of the touchscreen interface, and the ease with which operators can navigate through different menus and settings. Advanced HMIs may offer customizable displays that allow operators to prioritize the most relevant information for their specific applications. The ability to create and store multiple user profiles can be beneficial in environments where different operators may have varying levels of expertise or specific preferences. Additionally, features such as multi-language support and context-sensitive help functions can enhance usability, particularly in international manufacturing environments. Some friction stir welders incorporate advanced HMI features such as augmented reality overlays, which can provide visual guidance for tool positioning or display real-time weld quality indicators directly on the workpiece. The integration of remote access capabilities into the HMI can also be advantageous, allowing for off-site troubleshooting, software updates, and process optimization without the need for on-site technical support.
Data Acquisition Systems for Quality Monitoring
Data acquisition systems are integral components of modern friction stir welders, providing comprehensive monitoring and analysis capabilities that are essential for quality control and process optimization. These systems collect, process, and store a wide range of parameters throughout the welding process, including spindle speed, axial force, tool position, and temperature profiles. Advanced data acquisition systems may also incorporate real-time analysis algorithms that can detect anomalies or deviations from specified welding parameters, enabling immediate corrective actions to maintain weld quality. The data collected by these systems serves multiple purposes, from validating weld quality for critical applications to providing insights for continuous process improvement.
When evaluating friction stir welders, the capabilities of the data acquisition system should be closely examined to ensure alignment with quality control requirements and regulatory standards. Key considerations include the sampling rate of the system, which determines its ability to capture high-frequency variations in welding parameters. The storage capacity and data management features of the system are also crucial, particularly for applications requiring long-term data retention for traceability purposes. Advanced data acquisition systems may offer features such as real-time data visualization, allowing operators to monitor trends and correlations between different welding parameters. The ability to export data in standard formats for further analysis or integration with enterprise quality management systems can significantly enhance the value of the collected information. Some friction stir welders incorporate advanced data analysis tools directly into their control systems, providing features such as statistical process control (SPC) charts, weld quality prediction models, and automated report generation. These capabilities can streamline quality assurance processes and facilitate compliance with industry-specific standards and regulations.
Friction Stir Welder Maintenance and Upkeep
The maintenance and upkeep of friction stir welders are critical aspects that directly impact machine performance, weld quality, and operational efficiency. A well-maintained friction stir welder not only produces consistent, high-quality welds but also experiences reduced downtime and extended service life. Developing a comprehensive maintenance strategy requires consideration of various factors, including the machine's design, usage patterns, and the specific requirements of the welding applications. Regular maintenance activities typically encompass tasks such as tool inspection and replacement, spindle lubrication, and calibration of force and position sensors. More complex maintenance procedures may involve the alignment of machine axes, verification of machine geometry, and overhaul of critical components such as bearings and seals.
When selecting a friction stir welder, it is essential to evaluate the maintenance requirements and support options provided by the manufacturer. Some advanced friction stir welders incorporate self-diagnostic systems that can detect wear patterns, predict component failures, and schedule maintenance activities proactively. These predictive maintenance capabilities can significantly reduce unplanned downtime and optimize maintenance schedules. The availability of remote diagnostics and support services should also be considered, as these can facilitate rapid troubleshooting and minimize the need for on-site technical visits. Additionally, the modularity of machine components and the ease of access for maintenance tasks can greatly influence the efficiency of maintenance operations. Manufacturers should assess the availability and cost of spare parts, as well as the lead times for critical components, to ensure that maintenance activities can be carried out promptly without extended production interruptions.
Training and documentation provided by the friction stir welder manufacturer play a crucial role in effective maintenance and upkeep. Comprehensive operator and maintenance manuals, along with detailed troubleshooting guides, can empower in-house technicians to perform routine maintenance tasks and resolve common issues independently. Some manufacturers offer advanced training programs that cover not only basic maintenance procedures but also in-depth diagnostics and repair techniques. These training opportunities can be valuable investments in developing internal expertise and reducing reliance on external service providers. When evaluating friction stir welders, manufacturers should inquire about the availability of ongoing technical support, software updates, and access to knowledge bases or user communities that can provide additional resources for maintenance and troubleshooting.
Matching Friction Stir Welders to Application Requirements
The process of matching friction stir welders to specific application requirements is a critical step in ensuring optimal performance, efficiency, and cost-effectiveness in industrial welding operations. This process involves a detailed analysis of the intended applications, including material types, geometries, production volumes, and quality standards. By aligning the capabilities of the friction stir welder with the precise needs of the application, manufacturers can maximize the benefits of this advanced welding technology while minimizing unnecessary costs or operational complexities.
High-Volume Production Runs with Dedicated Machines
For high-volume production runs, dedicated friction stir welding machines offer significant advantages in terms of efficiency, consistency, and throughput. These machines are designed and optimized for specific welding tasks, often featuring custom fixturing, automated material handling systems, and specialized tooling. The primary benefit of dedicated machines is their ability to maintain high production rates while ensuring consistent weld quality across large batches. In automotive manufacturing, for example, dedicated friction stir welders might be employed for joining aluminum body panels or structural components, where the repetitive nature of the task justifies the investment in specialized equipment.
When considering dedicated friction stir welders for high-volume production, several factors must be evaluated. The machine's cycle time, including loading, welding, and unloading operations, should be carefully assessed to ensure it meets production targets. The level of automation in material handling and part positioning can significantly impact overall efficiency and labor requirements. Advanced dedicated machines may incorporate in-line quality control systems, such as automated ultrasonic testing or vision-based inspection, to ensure 100% quality verification without slowing production. The flexibility of the machine to accommodate minor variations in part geometry or welding parameters should also be considered, as even high-volume production may require occasional adjustments. Additionally, the integration capabilities of the dedicated friction stir welder with existing production lines and enterprise resource planning (ERP) systems can be crucial for optimizing overall manufacturing workflows and data management.
Flexible Welding Cells for Diverse Applications
Flexible welding cells offer a versatile solution for manufacturers dealing with a diverse range of friction stir welding applications. These cells typically consist of multi-axis friction stir welding machines, often integrated with robotic systems for enhanced flexibility in part handling and welding path execution. The key advantage of flexible welding cells is their ability to adapt to different part geometries, materials, and welding parameters with minimal changeover time. This versatility makes them particularly suitable for industries with frequent product changes or low to medium volume production runs, such as aerospace or custom fabrication.
When evaluating flexible friction stir welding cells, several critical factors should be considered. The working envelope of the machine, including the range of motion for each axis, determines the size and complexity of parts that can be welded. The ability to quickly change tooling and welding parameters between different applications is crucial for maintaining productivity in mixed production environments. Advanced flexible cells may incorporate features such as automatic tool changing systems and programmable fixturing to further reduce setup times. The control system of the flexible cell plays a vital role in its adaptability, with advanced systems offering features such as offline programming capabilities, simulation tools for process optimization, and integration with CAD/CAM systems for seamless workflow from design to production. Additionally, the scalability of the flexible cell should be assessed, considering factors such as the ability to add additional axes or integrate with other manufacturing processes in the future.